In industrial applications, laser beam quality plays a pivotal role in determining the efficiency, precision, and overall success of laser-based processes. From cutting and welding to marking and engraving, the quality of the laser beam directly impacts the performance and outcomes of various operations. Understanding and optimizing laser beam quality are critical for industries aiming to achieve high standards of productivity and reliability.
What is Laser Beam Quality?
Laser beam quality refers to the characteristics of a laser beam that determine its performance in a given application. Key parameters include:
- Beam Divergence: The rate at which the laser beam spreads as it travels. Lower divergence indicates better focus over longer distances.
- Beam Profile: The spatial distribution of intensity across the beam, often described as Gaussian or multimode.
- M² Factor (Beam Quality Factor): A numerical value representing how closely a beam approximates an ideal Gaussian beam. An M² of 1 indicates the best possible quality.
Why is Laser Beam Quality Important?
1. Precision and Accuracy
High beam quality ensures focused energy delivery, enabling precise cuts, welds, or markings.
- Example: In micromachining, a well-focused beam allows for intricate designs and minimal material distortion.
- Impact: Poor beam quality leads to rough edges, inconsistencies, and defects in the final product.
2. Efficiency in Material Processing
Laser processes such as cutting and welding benefit from concentrated energy, reducing waste and increasing throughput.
- Cutting: A high-quality beam achieves cleaner cuts with minimal heat-affected zones.
- Welding: Enhanced beam quality ensures deeper penetration and stronger joints.
3. Reduced Downtime and Costs
Optimized beam quality minimizes errors and material wastage, leading to cost savings and less downtime for adjustments or rework.
Applications of Laser Beam Quality in Industries
1. Manufacturing and Fabrication
High-quality laser beams are indispensable for precise material cutting, drilling, and engraving.
- Metals: Produces smooth edges and detailed engravings.
- Non-metals: Processes materials like plastics, ceramics, and composites with minimal damage.
2. Automotive Industry
Lasers are used for welding critical components like body panels and battery enclosures in electric vehicles.
- Beam Quality Impact: Ensures consistent weld strength and reduces failure rates in safety-critical parts.
3. Electronics
In electronics manufacturing, laser beam quality is crucial for tasks like PCB drilling and micro-welding.
- High Precision: Supports miniaturization trends by creating intricate and accurate patterns.
4. Aerospace
Laser systems with superior beam quality are used for cutting, welding, and additive manufacturing of lightweight and durable aerospace components.
5. Medical Device Manufacturing
Laser machining of medical devices, such as stents and surgical tools, demands high beam quality for intricate designs and tight tolerances.
Factors Affecting Laser Beam Quality
1. Laser Type
Different types of lasers, such as COâ‚‚, fiber, and diode lasers, offer varying levels of beam quality.
- Fiber Lasers: Known for excellent beam quality and high precision.
- COâ‚‚ Lasers: Ideal for processing non-metals but may have lower beam quality compared to fiber lasers.
2. Optical Components
Lenses, mirrors, and coatings in the laser system influence the beam’s focus and consistency.
- Maintenance: Regular cleaning and alignment ensure optimal performance.
3. Beam Delivery System
The system delivering the laser beam, including fibers and optics, must preserve beam quality to achieve desired results.
4. Power Stability
Fluctuations in laser power can degrade beam quality, leading to inconsistent processing outcomes.
Measuring Laser Beam Quality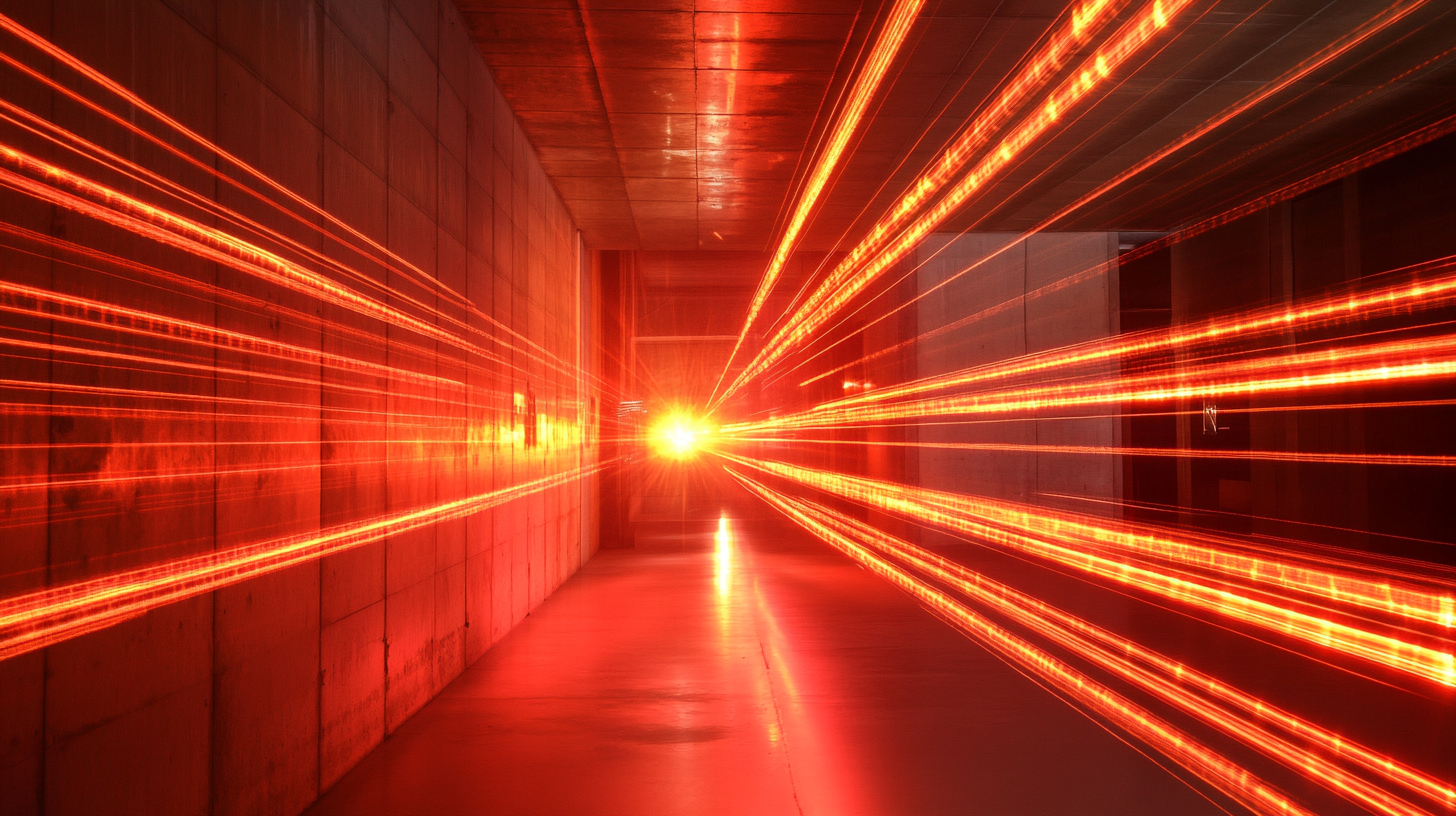
1. Beam Profiling
Analyzes the intensity distribution and shape of the beam.
- Tools: Beam profilers and cameras.
- Usage: Identifies irregularities and enables adjustments.
2. M² Measurement
Quantifies the deviation of a laser beam from an ideal Gaussian beam.
- Application: Ensures the laser system meets the required quality standards.
3. Spot Size and Focus Testing
Determines the sharpness and size of the laser spot at its focal point.
Improving Laser Beam Quality
1. Regular Maintenance
Cleaning and aligning optical components reduce beam distortions.
2. Advanced Cooling Systems
Maintains temperature stability, preventing thermal effects that degrade beam quality.
3. Upgraded Laser Sources
Investing in modern lasers with better M² values ensures superior performance.
4. Enhanced Beam Delivery Systems
Using high-quality optics and fibers preserves beam integrity.
Future Trends in Laser Beam Quality
1. Adaptive Optics
Real-time adjustments to beam properties enhance precision and adaptability for complex applications.
2. AI-Driven Quality Monitoring
Artificial intelligence enables predictive maintenance and real-time optimization of beam quality.
3. Ultrafast Lasers
Developments in femtosecond and picosecond lasers offer unprecedented precision and minimal heat effects.
Conclusion
The quality of a laser beam is a critical determinant of success in industrial applications. High beam quality enhances precision, efficiency, and cost-effectiveness, making it indispensable for cutting-edge manufacturing processes. By understanding and optimizing beam parameters, industries can achieve superior outcomes and remain competitive in an increasingly demanding market.