Fiber Lasers: A Game Changer for Cutting and Welding
Fiber lasers have revolutionized the fields of cutting and welding due to their superior efficiency, precision, and versatility. Unlike traditional CO₂ or solid-state lasers, fiber lasers offer significant advantages in various industrial applications, particularly in metal processing, automotive, aerospace, and manufacturing industries. Here’s a detailed look at why fiber lasers are considered a game changer for cutting and welding.
What Are Fiber Lasers?
A fiber laser is a type of solid-state laser where the active gain medium is an optical fiber doped with rare-earth elements such as ytterbium, erbium, or neodymium. The laser beam is generated inside the fiber core, which guides and amplifies the light. The key feature of fiber lasers is the use of fiber optics for beam delivery, making them compact, flexible, and highly efficient.
Key Advantages of Fiber Lasers for Cutting and Welding
- High Efficiency:
- Fiber lasers are much more energy-efficient than traditional CO₂ and Ndlasers. They convert a higher percentage of electrical energy into laser light, typically boasting 30-40% efficiency, compared to around 10% for CO₂ lasers.
- This high efficiency leads to lower operating costs and reduced energy consumption, which is crucial for industrial applications that require continuous operation.
- Superior Beam Quality:
- Fiber lasers provide excellent beam quality, with a smaller focused spot size and higher power density. This results in more precise cuts and cleaner welds.
- The high beam quality allows fiber lasers to cut through thin and thick materials with ease, offering versatility for a wide range of applications.
- Speed and Precision:
- In cutting applications, fiber lasers offer significantly faster cutting speeds compared to CO₂ lasers, particularly in thin to medium-thickness metals. The high energy density and sharp focus of the beam enable rapid and clean cutting, with minimal material waste.
- For welding, fiber lasers provide deep penetration and narrow weld seams, making them ideal for high-precision applications where accuracy is critical.
- Versatility in Materials:
- Fiber lasers can process a variety of materials, including metals like stainless steel, carbon steel, aluminum, copper, brass, and titanium. This versatility makes them suitable for industries that work with multiple materials.
- They are also excellent at processing reflective metals (such as copper and aluminum), which are more challenging for CO₂ lasers due to the risk of back reflections damaging the machine.
- Lower Maintenance Costs:
- Fiber lasers have a simpler and more robust design than CO₂ lasers. Since fiber lasers don’t rely on mirrors or gas-filled tubes, there are fewer moving parts, leading to less wear and tear and lower maintenance requirements.
- The sealed fiber optic delivery system also means there is no need for beam alignment or cleaning of optical components, which can be time-consuming with other types of lasers.
- Compact Size and Flexibility:
- The compact design of fiber lasers makes them more adaptable to a wide range of industrial setups. They can be integrated into robotic systems or multi-axis CNC machines for automated cutting and welding processes.
- Fiber lasers also allow for long-distance beam delivery without significant power loss, making them ideal for flexible and remote applications.
- High Power Output:
- Fiber lasers are available in a wide range of power levels, from low-power systems (for fine, precise work) to high-power lasers (for cutting thick metals and heavy-duty welding).
- High-power fiber lasers (in the kilowatt range) are capable of cutting through thick metal sheets (up to 50 mm or more) and performing deep-penetration welding on heavy materials, offering unmatched performance in demanding applications.
- Environmental Benefits:
- Fiber lasers do not require the use of laser gases (as CO₂ lasers do), which reduces their environmental impact and operational costs. They also generate less heat, requiring less cooling and reducing overall energy consumption.
- The precision and efficiency of fiber lasers lead to less material waste during cutting and welding processes, contributing to a more sustainable manufacturing process.
Cutting with Fiber Lasers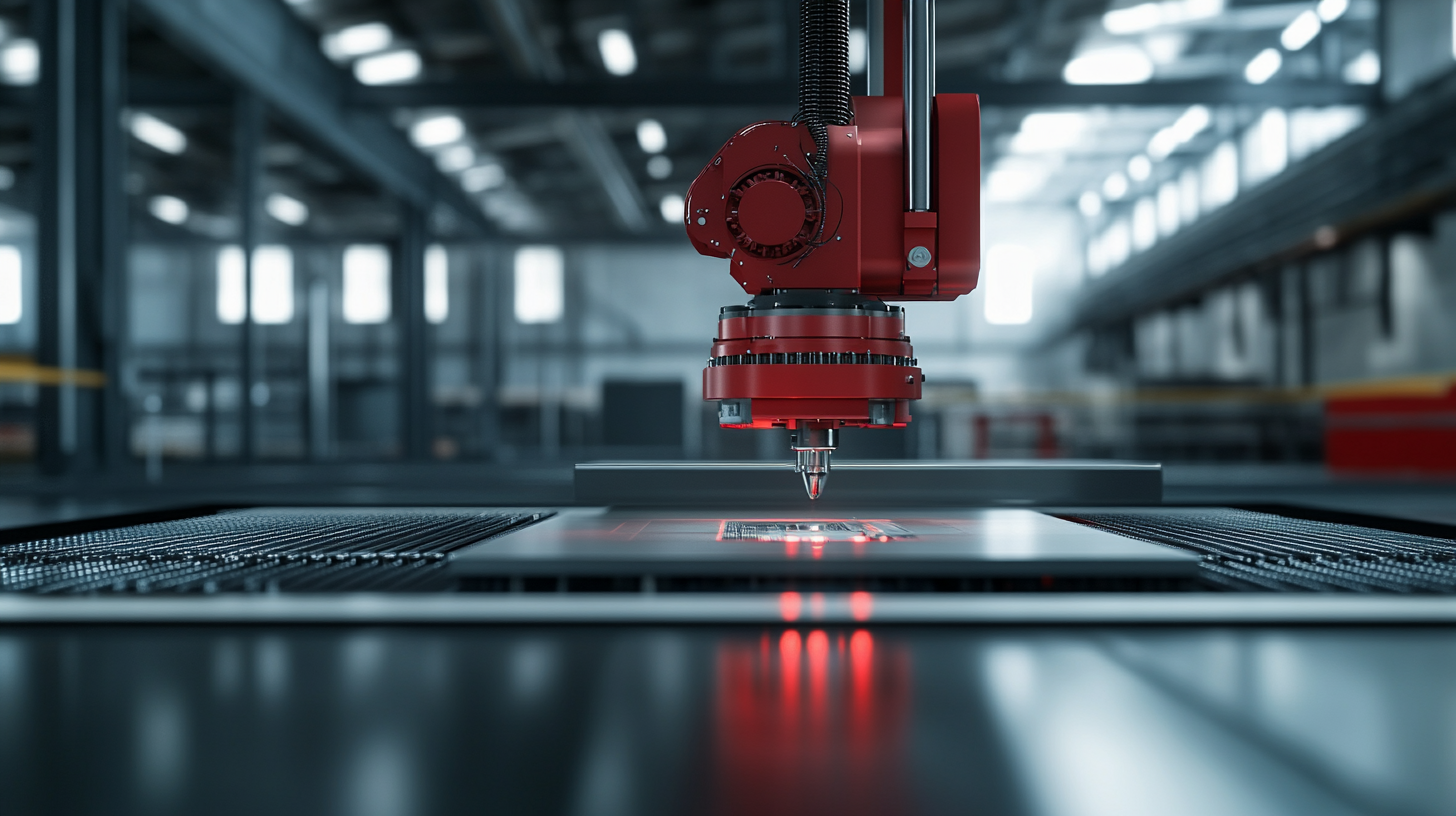
Fiber lasers are widely used for cutting because of their ability to produce high-quality cuts with minimal thermal distortion. Here are some specific advantages when using fiber lasers for cutting:
- Speed: Fiber lasers can cut materials faster than CO₂ lasers, particularly for thin metals. This increases throughput in industrial environments.
- Edge Quality: Fiber lasers produce smooth, clean edges with minimal burrs, reducing the need for post-processing.
- Minimal Heat-Affected Zone (HAZ): The high focus and precision of the fiber laser beam create a small heat-affected zone, which preserves the integrity of the surrounding material and prevents warping.
Welding with Fiber Lasers
In welding applications, fiber lasers offer strong, precise welds with excellent penetration depth. Key benefits include:
- Deep Penetration: Fiber lasers can achieve deep welds with narrow weld seams, making them ideal for applications where high strength is required.
- Reduced Distortion: The concentrated heat of the laser beam minimizes thermal distortion, allowing for tight tolerances and consistent welds.
- Automated Welding: Fiber lasers are easily integrated into robotic welding systems for high-volume, automated welding in industries such as automotive, aerospace, and electronics.
Applications of Fiber Lasers in Cutting and Welding
- Automotive Industry:
- Fiber lasers are used for cutting and welding car bodies, chassis components, and exhaust systems. Their precision and speed allow manufacturers to meet tight production schedules while ensuring quality.
- Aerospace:
- In aerospace, fiber lasers are used for cutting and welding lightweight alloys and other advanced materials used in aircraft and spacecraft construction. The high precision ensures structural integrity and safety.
- Metal Fabrication:
- Metal fabricators use fiber lasers for cutting sheet metal, tubes, and pipes for a variety of products, from furniture to industrial machinery. Fiber lasers are ideal for custom fabrication due to their flexibility.
- Electronics Industry:
- Fiber lasers are used for microwelding in the electronics industry, where tiny, precise welds are required for components such as batteries, connectors, and sensors.
Conclusion
Fiber lasers have emerged as a game changer in cutting and welding applications due to their efficiency, precision, low maintenance, and versatility. They outperform traditional lasers in nearly every aspect, making them the preferred choice for many industries. With continued advancements in fiber laser technology, we can expect further improvements in speed, power, and cost-effectiveness, driving even greater adoption across a broad range of applications.
Switching to fiber laser technology can result in higher productivity, improved product quality, and lower operating costs, making it a smart investment for companies in industries like automotive, aerospace, electronics, and metal fabrication.