In industrial environments, LED lighting must operate reliably under harsh conditions such as high temperatures, dust, moisture, and electrical fluctuations. Selecting the right LED power supply ensures stable performance, longevity, and energy efficiency while minimizing downtime and maintenance costs. This guide outlines the key factors to consider when choosing LED power supplies for industrial applications.
1. Understand Power Supply Types
Constant Voltage Power Supplies
- Designed for LED systems requiring a steady voltage output, such as LED strips or low-voltage fixtures.
- Common output options: 12V and 24V DC.
Constant Current Power Supplies
- Deliver a steady current (e.g., 350mA, 700mA) for systems where LED brightness depends on current regulation.
- Ideal for high-power LEDs used in industrial fixtures.
Tip: Understand your lighting system’s electrical needs to determine the appropriate type of driver.
2. Power and Efficiency Requirements
Wattage Capacity
- Calculate the total power required by your LED system, then choose a power supply with 20-30% higher wattage capacity.
- Overloading leads to overheating and reduced lifespan.
Efficiency Rating
- Industrial applications demand highly efficient power supplies (efficiency >85%) to reduce energy loss and operating costs.
- Look for energy-saving certifications like ENERGY STAR or 80 PLUS.
Power Factor (PF)
- A high power factor (≥0.9) ensures energy is used efficiently, reducing strain on electrical systems.
3. Durability and Protection Ratings
Ingress Protection (IP) Ratings
Industrial environments often involve exposure to dust, moisture, and chemicals. Choose a power supply with:
- IP65: Dust-tight and resistant to water jets.
- IP67: Dust-tight and immersion-proof for short periods.
- IP68: Protection against continuous submersion in water.
Operating Temperature Range
- Verify the power supply can withstand temperature fluctuations, typically -40°C to +70°C in industrial settings.
Vibration Resistance
- Power supplies with rugged casings and vibration-proof designs are necessary for factories or heavy machinery environments.
Surge and Overvoltage Protection
- Industrial power supplies should include surge protection to handle voltage spikes caused by heavy equipment or power grid disturbances.
4. Compatibility with Control Systems
Modern industrial environments often use advanced lighting control systems to optimize energy usage and productivity.
Dimming Capabilities
- Choose power supplies that support industrial dimming protocols like:
- 0-10V Dimming: Simple and reliable analog dimming.
- PWM (Pulse Width Modulation): Ensures smooth, flicker-free dimming.
- DALI (Digital Addressable Lighting Interface): Offers precise control and real-time feedback for smart lighting systems.
Smart Lighting Integration
- For IoT-based systems, ensure compatibility with wireless protocols like Zigbee, Bluetooth Mesh, or Wi-Fi.
5. Safety and Compliance
Industrial power supplies must comply with stringent safety and regulatory standards to ensure worker safety and system reliability. Look for:
- UL Certification (Underwriters Laboratories)
- CE Marking (European safety standards)
- RoHS Compliance (Restriction of Hazardous Substances)
- EMI/EMC Compliance (Electromagnetic interference and compatibility)
6. Reliability and Maintenance Considerations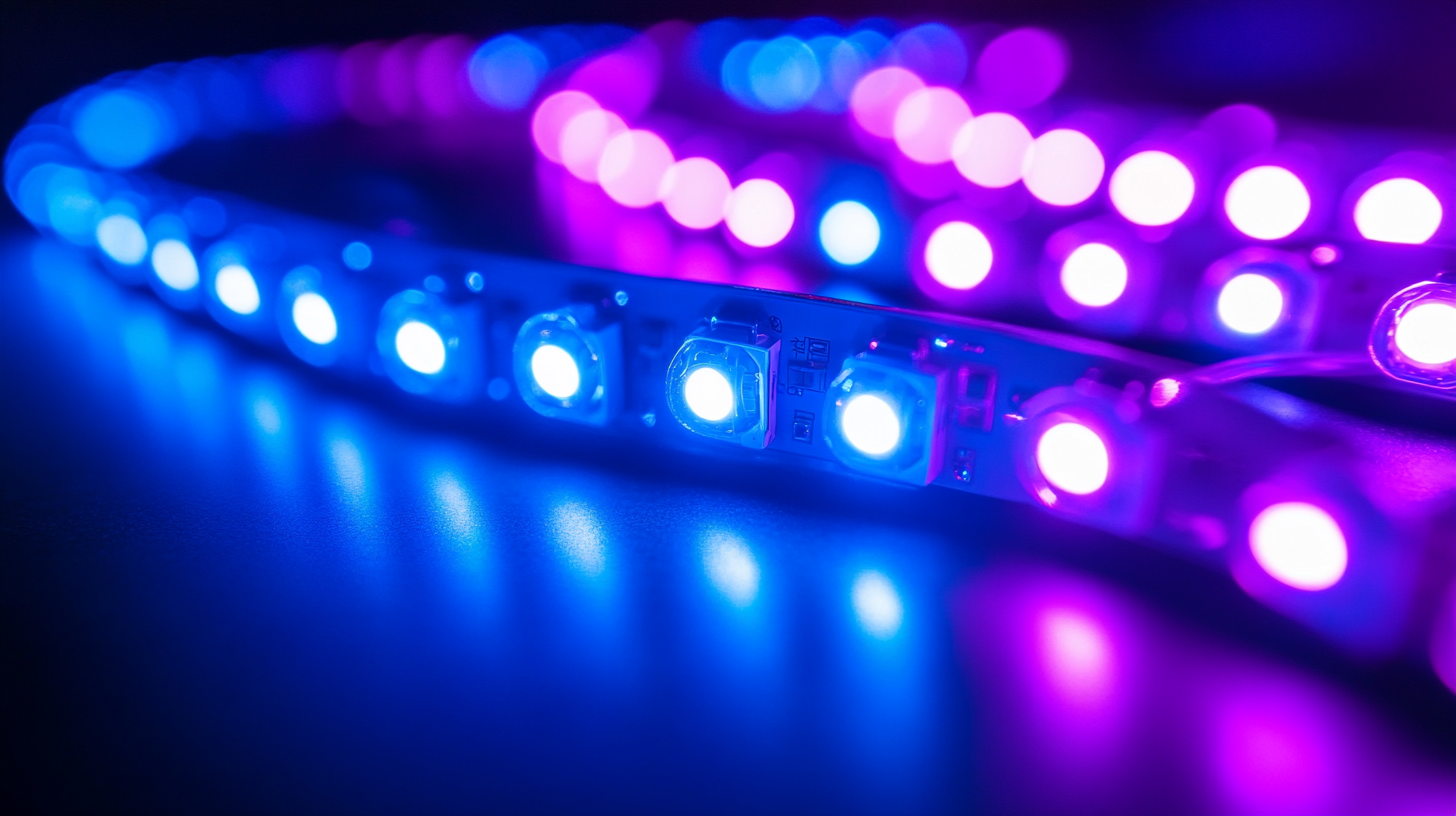
Thermal Management
- Overheating can lead to power supply failure. Opt for units with:
- Heat Sinks: Dissipate excess heat.
- Fanless Cooling: Reduces noise and mechanical failure risks.
Redundancy Features
- In mission-critical applications, choose power supplies with failover redundancy or parallel operation for uninterrupted performance.
Low Total Harmonic Distortion (THD)
- A THD of <20% ensures clean power output, reducing electrical interference and improving system efficiency.
7. Application-Specific Factors
Harsh Environments
- Power supplies in manufacturing plants, foundries, and chemical plants must withstand extreme heat, corrosive elements, and debris.
Outdoor Industrial Use
- For facilities like loading docks or construction zones, IP67-rated power supplies with surge protection are ideal.
High-Bay Lighting Systems
- Opt for reliable constant-current power supplies with long operating lifespans to reduce maintenance in hard-to-access areas.
8. Longevity and Warranty
- Industrial-grade LED power supplies should offer MTBF (Mean Time Between Failures) ratings exceeding 50,000 hours.
- Look for warranties of 5 years or more to ensure product reliability and manufacturer confidence.
Checklist for Choosing an LED Power Supply for Industrial Use
- Electrical Requirements: Wattage, voltage, and current compatibility.
- Durability: IP rating, operating temperature, and vibration resistance.
- Energy Efficiency: High power factor, low THD, and certifications.
- Control Features: Dimming and smart lighting integration.
- Safety Standards: Compliance with UL, CE, RoHS, and EMI/EMC regulations.
- Thermal Management: Heat sinks and fanless designs.
- Maintenance: Long lifespan, redundancy, and reliability features.
Conclusion
Selecting the right LED power supply for industrial environments requires careful consideration of durability, electrical performance, energy efficiency, and compatibility with advanced controls. A high-quality power supply ensures reliable lighting performance, reduces energy costs, and minimizes downtime, making it a valuable investment for industrial operations.