CO₂ lasers have become a cornerstone of industrial manufacturing, offering precision, speed, and versatility. These lasers operate in the infrared spectrum and are highly efficient for cutting, engraving, and welding a wide range of materials. This article explores the diverse applications of CO₂ lasers in industrial manufacturing and their benefits for production processes.
1. Cutting Applications
CO₂ lasers are widely used for precision cutting due to their ability to handle a variety of materials with high accuracy.
Materials Cut with CO₂ Lasers
- Metals: Thin sheets of stainless steel, aluminum, and mild steel.
- Non-Metals: Wood, acrylic, plastics, leather, paper, and textiles.
Key Benefits
- Clean, smooth edges with minimal post-processing.
- High-speed cutting for increased productivity.
- Non-contact process that reduces material deformation.
Industries
- Automotive: Cutting interior components and body panels.
- Electronics: Precision cutting for circuit boards and enclosures.
2. Engraving and Marking
CO₂ lasers excel in creating detailed engravings and permanent markings, making them ideal for branding, labeling, and decorative purposes.
Applications
- Engraving: Logos, text, and intricate designs on materials like glass, wood, and leather.
- Marking: Serial numbers, barcodes, and QR codes for traceability.
Industries
- Packaging: Marking expiration dates and batch numbers on products.
- Jewelry: Custom engravings on metals and gemstones.
3. Welding
CO₂ lasers provide precise and efficient welding for metals and non-metals, ensuring strong and durable joints.
Applications
- Welding thin metal sheets in automotive and aerospace industries.
- Joining dissimilar materials, such as plastics and composites.
Key Benefits
- Minimal heat-affected zones reduce material distortion.
- High-speed welding for increased production efficiency.
4. Surface Treatment
CO₂ lasers are used to modify or enhance surface properties for improved performance and durability.
Techniques
- Laser Hardening: Strengthens the surface of metals by altering their microstructure.
- Texturing: Creates patterns on surfaces to improve grip or adhesion.
- Cleaning: Removes rust, paint, and contaminants without damaging the substrate.
Industries
- Tooling: Surface hardening of cutting tools and molds.
- Automotive: Surface texturing for improved paint adhesion.
5. Additive Manufacturing (3D Printing)
CO₂ lasers are integral to certain additive manufacturing processes, such as selective laser sintering (SLS).
Applications
- Producing complex parts and prototypes from polymers and composites.
- Rapid manufacturing of components with intricate geometries.
Key Benefits
- High precision and repeatability.
- Ability to work with a wide range of materials.
6. Drilling
CO₂ lasers provide high-precision drilling capabilities, especially for small-diameter holes in delicate materials.
Applications
- Micro-drilling in electronic components like printed circuit boards (PCBs).
- Drilling holes in ceramics and composites for aerospace and medical devices.
Advantages
- Consistent hole quality with minimal material wastage.
- High-speed drilling for large-scale production.
7. Cutting and Welding in Textile Manufacturing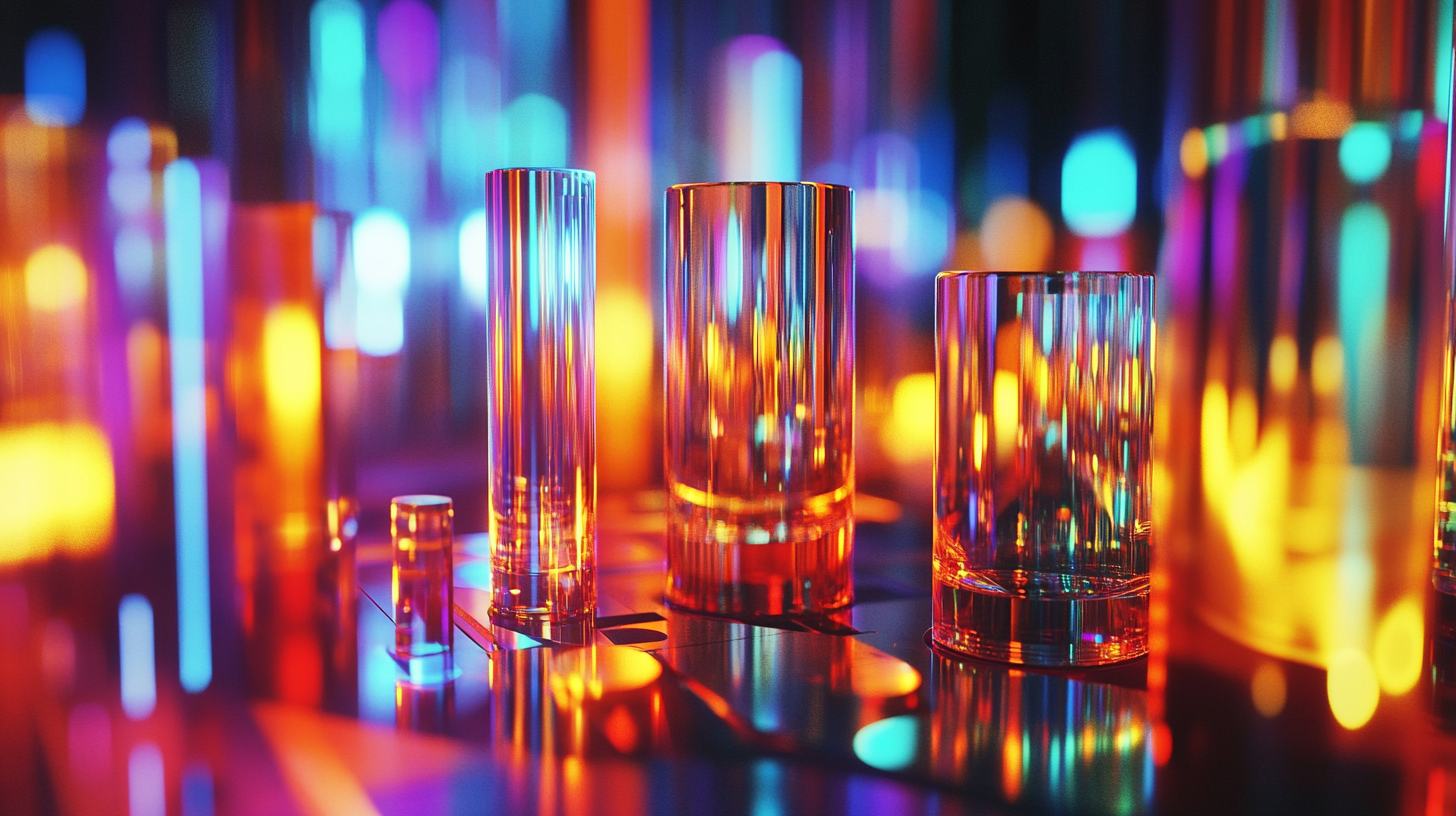
CO₂ lasers are extensively used in the textile industry for their ability to cut and seal fabrics simultaneously.
Applications
- Cutting synthetic fabrics like polyester and nylon.
- Creating intricate patterns and designs for fashion and upholstery.
Key Benefits
- Prevents fraying by sealing fabric edges during cutting.
- Increases production speed and precision.
Advantages of CO₂ Lasers in Manufacturing
- Versatility
- Suitable for a wide range of materials and applications.
- Precision and Accuracy
- Enables detailed cuts, engravings, and modifications with minimal error.
- Non-Contact Processing
- Reduces wear and tear on tools, ensuring consistent quality over time.
- Energy Efficiency
- CO₂ lasers are highly efficient, offering cost savings in energy usage.
- High-Speed Operation
- Increases throughput in production environments, reducing lead times.
Challenges in Using CO₂ Lasers
- Material Limitations
- Not suitable for thick metals compared to fiber lasers.
- Initial Costs
- High setup costs for laser systems and associated equipment.
- Maintenance
- CO₂ lasers require periodic alignment and replacement of optical components.
Future Trends in CO₂ Laser Applications
- Integration with Automation
- CO₂ lasers are increasingly being paired with robotics for fully automated production lines.
- Advanced Control Systems
- AI-driven control systems will optimize laser parameters for enhanced efficiency and quality.
- Hybrid Manufacturing
- Combining CO₂ lasers with other technologies, such as 3D printing and CNC machining, for versatile manufacturing solutions.
Conclusion
CO₂ lasers are indispensable tools in industrial manufacturing, offering unmatched precision and versatility. From cutting and welding to engraving and surface treatment, their applications span diverse industries, enhancing efficiency and product quality. As technology evolves, CO₂ lasers will continue to play a pivotal role in shaping the future of manufacturing.